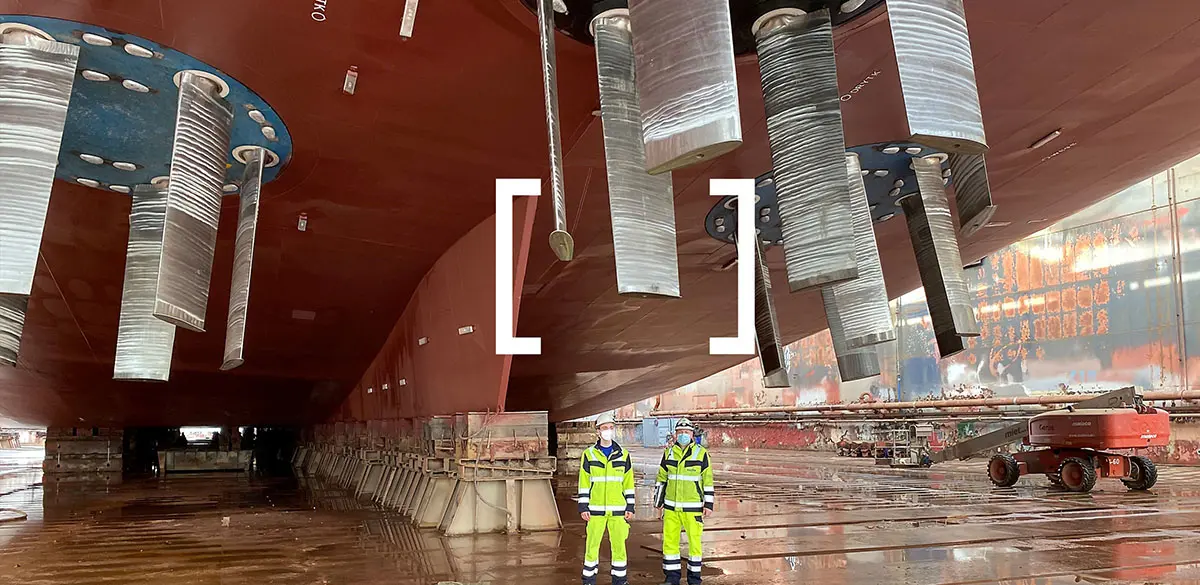
Servicing the giant
5 VSPs completely overhauled in 7 weeks
To date, it is the largest and most powerful vessel that Voith has equipped with its unique propulsion system, the Voith Schneider Propeller (VSP).
The “North Sea Giant” is an offshore construction vessel (OSV). This multi-purpose vessel is needed for long-term deployments in the field of offshore sub-sea construction. At 161 meters long and 30 meters wide, the vessel not only accommodates a crew of up to 199 people. Its large carrying capacity of 14,200 tons means that appropriate preliminary works can be carried out on the ship with the two built-in cranes, one with a capacity of 400 tons and 3,000 meters single line wire, the other with a capacity of 50 tons and 2,000 meters single line wire.
Making sure that the ship’s crew can arrive and do their job safely at the site of the sub-sea works in the first place are five VSPs with equally huge dimensions: Every single blade on a VSP is 3.6 m long. The diameter of the size 36 VSP used on this vessel is around 4.5 m. Two of these VSPs are located in the bow of the North Sea Giant and another three in the stern. And each of them has an output of 3,800 kW (5,160 hp). They propel the steel giant to a speed of 16 knots. But what’s much more important is that they are responsible for enabling the vessel to be positioned dynamically at sea even at wind force 8.
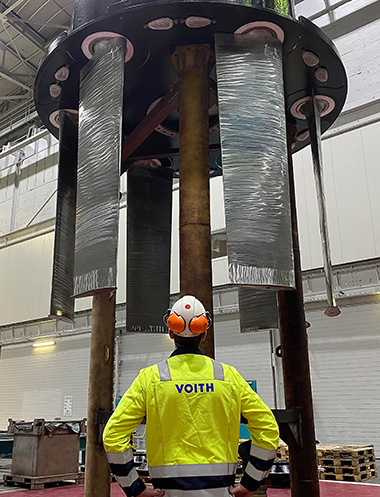
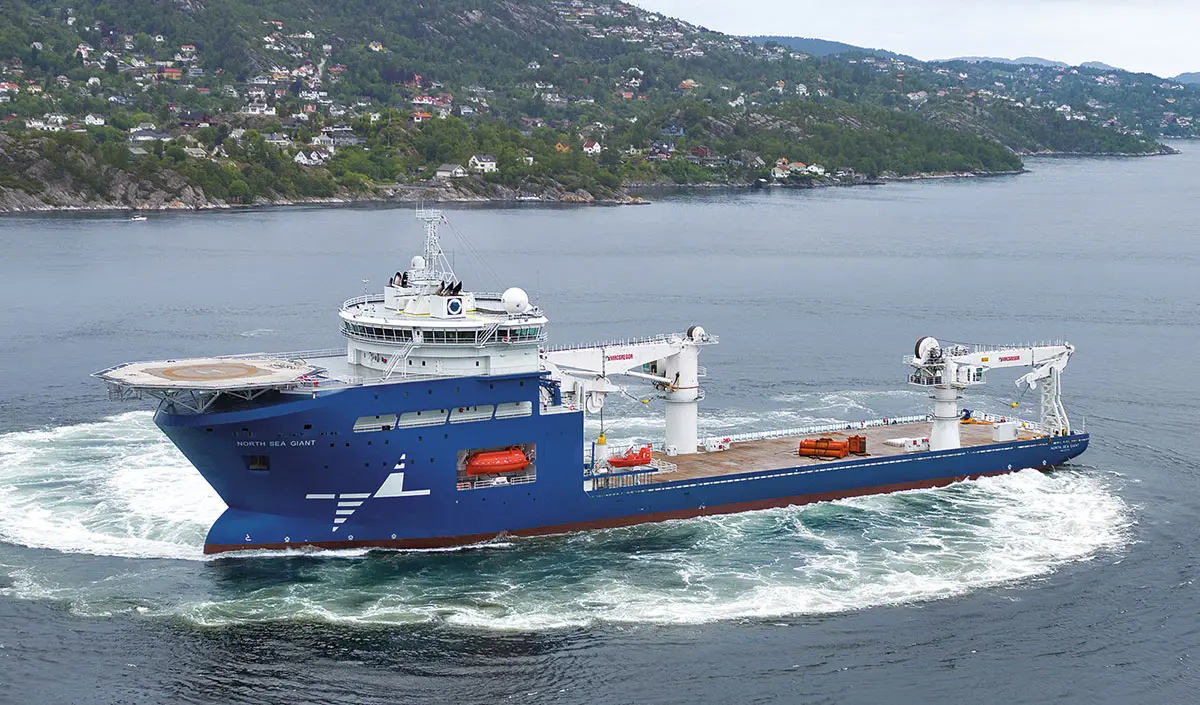
For 10 years, the North Sea Giant had been sailing across the North Sea, Baltic Sea and the Atlantic, accumulating a sensational 50,000 hours in operation. The time had finally come for the propulsion systems to be overhauled for the first time. This was a case for the Voith Offshore Team with Offshore Manager Andreas von Fintel and Field Assembly Supervisor Raphael Zonneveld, who took a year to prepare for the estimated seven-week deployment.
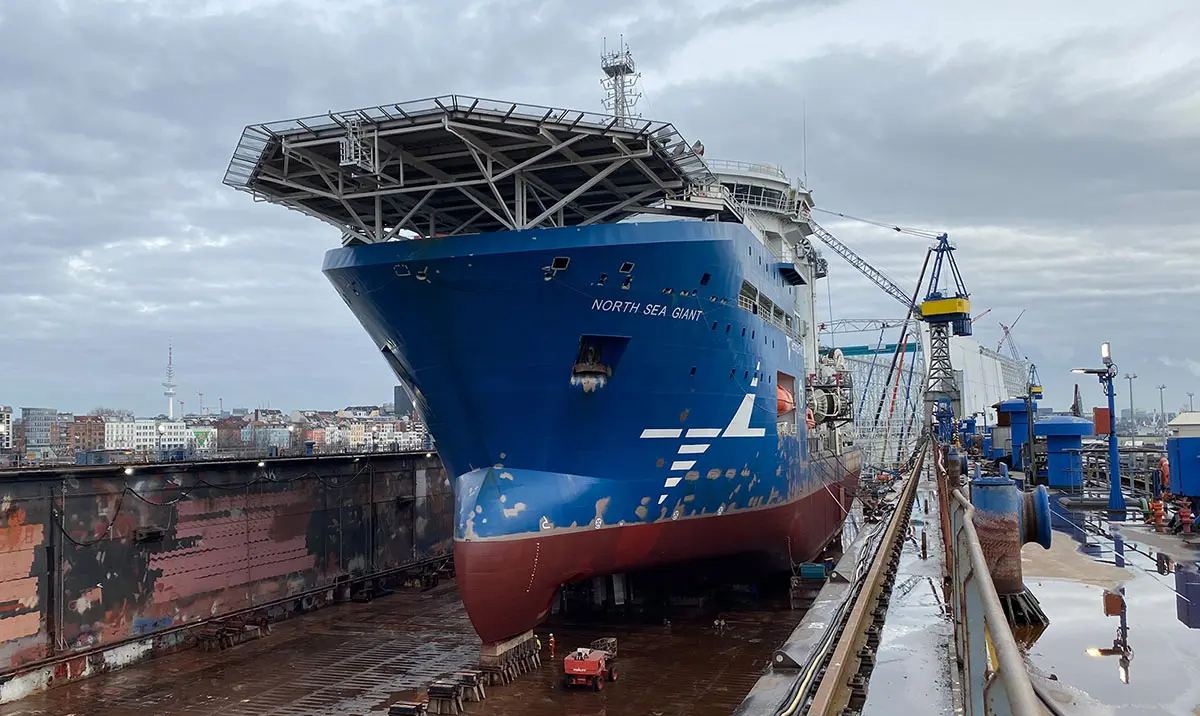
Two-shift operation due to COVID-19
“We held the kick-off meeting with the shipyard before Christmas. And then on January 4, we started on what was our largest-ever servicing contract for the maintenance and overhaul of the five VSPs,” says Zonneveld. At this point in time, the North Sea Giant was already in the floating dock at Blohm+Voss in the Port of Hamburg.
As field supervisor and chief fitter, Zonneveld coordinated the work of his team and the 20 dock workers for the North Sea Giant every day except on weekends. He did so under challenging conditions. Because of the global pandemic, “I had to split the teams into two shifts. This was the only way to ensure that we would stick to the hygiene rules and at the same time work efficiently,” he stresses.
Social distancing and mask-wearing rules applied, because despite the huge size of the vessel, the service technicians had to get close to one another as they worked. “Even with such a large ship, there were situations where it all came down to the very last millimeter,” says Zonneveld. Over the seven-week period starting on January 4, the team painstakingly worked through a total of 1,705 work steps from the project schedule. Every project stage had a time window that had to be met. At the daily “toolbox meeting,” which took place at 6 am every morning on the North Sea Giant, Zonneveld explained the schedule for the day to his service team. Then at 9 am he had another meeting with the shipyard workers to effectively coordinate the activities.
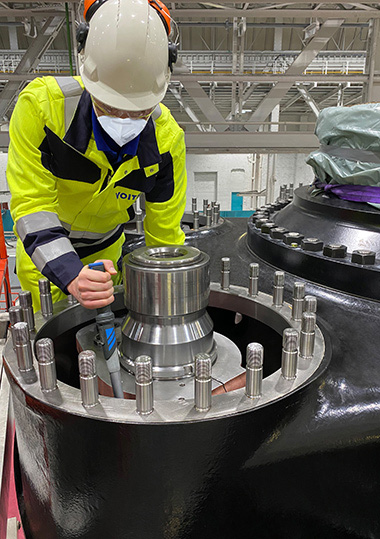
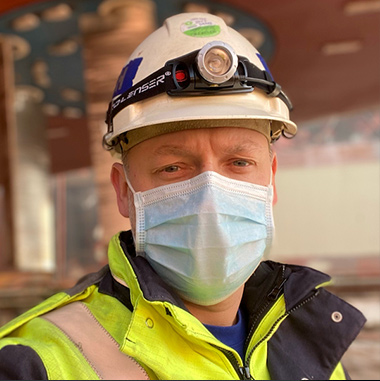
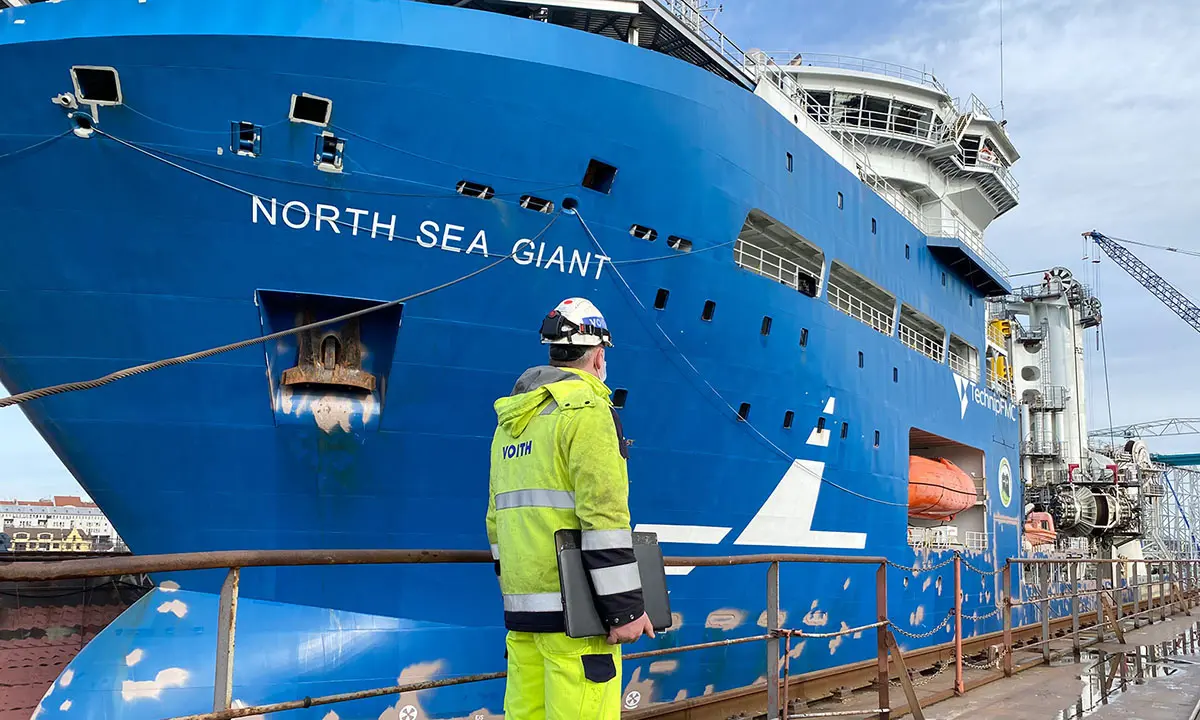
Precision work with 45 tons of machinery
On a cool February morning, the two teams were facing a special challenge. An opening had to be cut out of the ship’s hull to be able to remove one of the five VSPs. But despite what you would think given the dimensions of this giant steel structure, the cut-out was not going to expose an enormous cavity in the body of the vessel.
“We went straight through to the ship’s gym,” explains Zonneveld. And that’s not all: To be able to remove the 45 t wheel body of the VSP within the eight hours provided for in the project schedule, guide rails had to be installed and slinging points for the chain hoists welded on. It took two shifts. Finally, the second shift was able to very cautiously lower the wheel body, attached to three chain hoists, out of the ship’s hull.
The maintenance and overhaul as such could now begin. The VSP was dismantled into its individual components. The gearbox was checked for hairline cracks using ultrasound. The Voith service team subjected all wear parts to a special check under the critical eye of Raphael Zonneveld. In the last 20 years, he has overhauled many VSPs in ferries, tugs and platform supply vessels. “The gearbox and hydraulics of the VSPs were in peak condition. You would never know that they had notched up 50,000 hours in operation,” says Zonneveld. Nevertheless, gaskets were replaced, all hydraulic cylinders overhauled and the control system recalibrated.

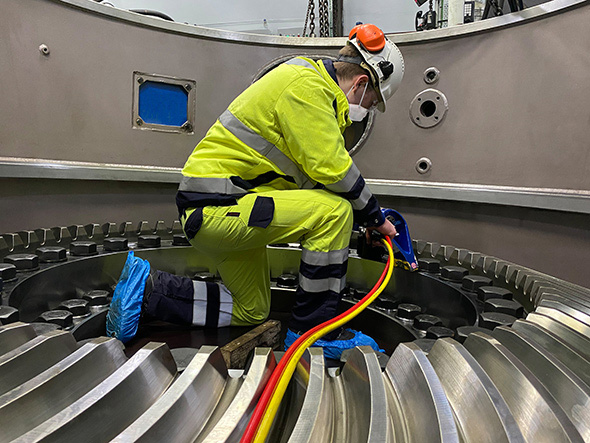
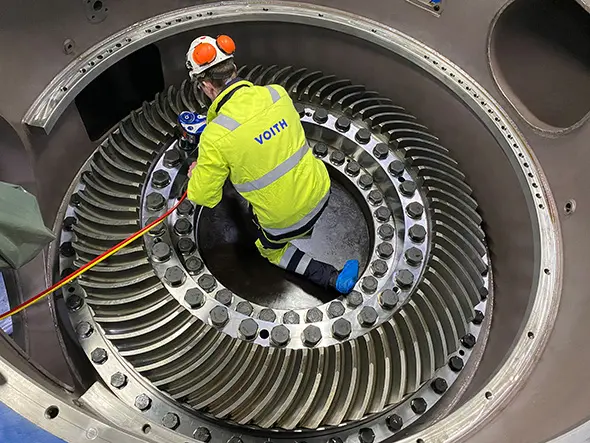
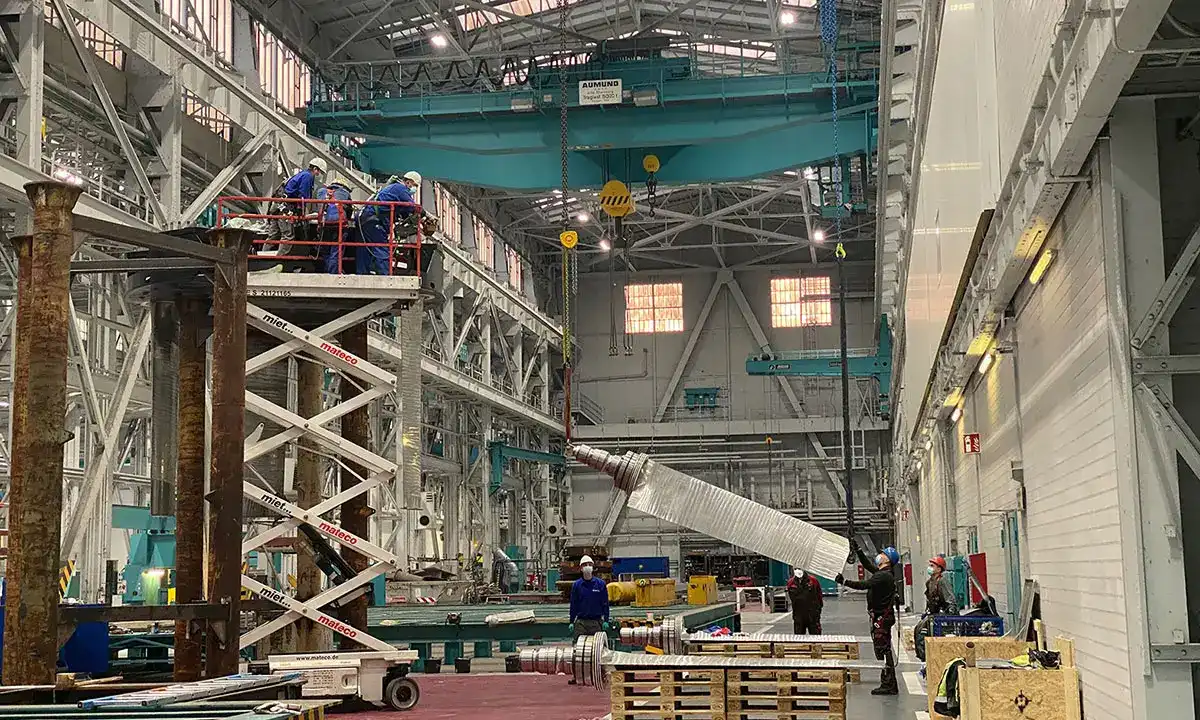
Tension before leaving the dock
The service work in the floating dry dock went according to plan. In the last six weeks, all five propellers were removed from the hull, overhauled, reassembled and reinstalled in the hull. Welding and painting work happened concurrently. The North Sea Giant’s hull started to take shape again, so a date for undocking could be set.
“This undocking process was very time-consuming and needed detailed preparation,” says Zonneveld. The inspection and acceptance process was then initiated. Not only was the entire maintenance crew on board (who incidentally lived on the ship in the dry dock over the entire seven weeks) but also representatives of the bodies that certify the acceptance and seaworthiness of the vessel, much like the German technical inspectorate TÜV does for road vehicles. The first step was to check for leaks after the ship was floated out into the water. Raphael Zonneveld says he had a sleepless night before this process of putting the ship back into the water. “I couldn‘t help it, but whenever all the servicing work on the vessel had been completed and we were waiting on the test run, I slept badly.”
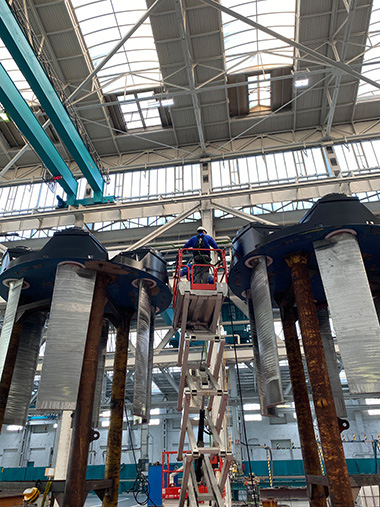
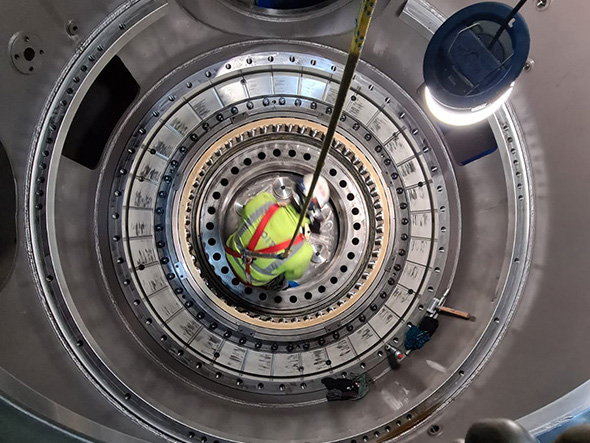
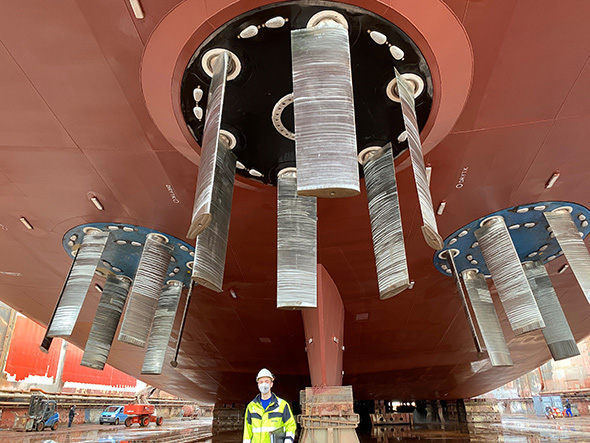
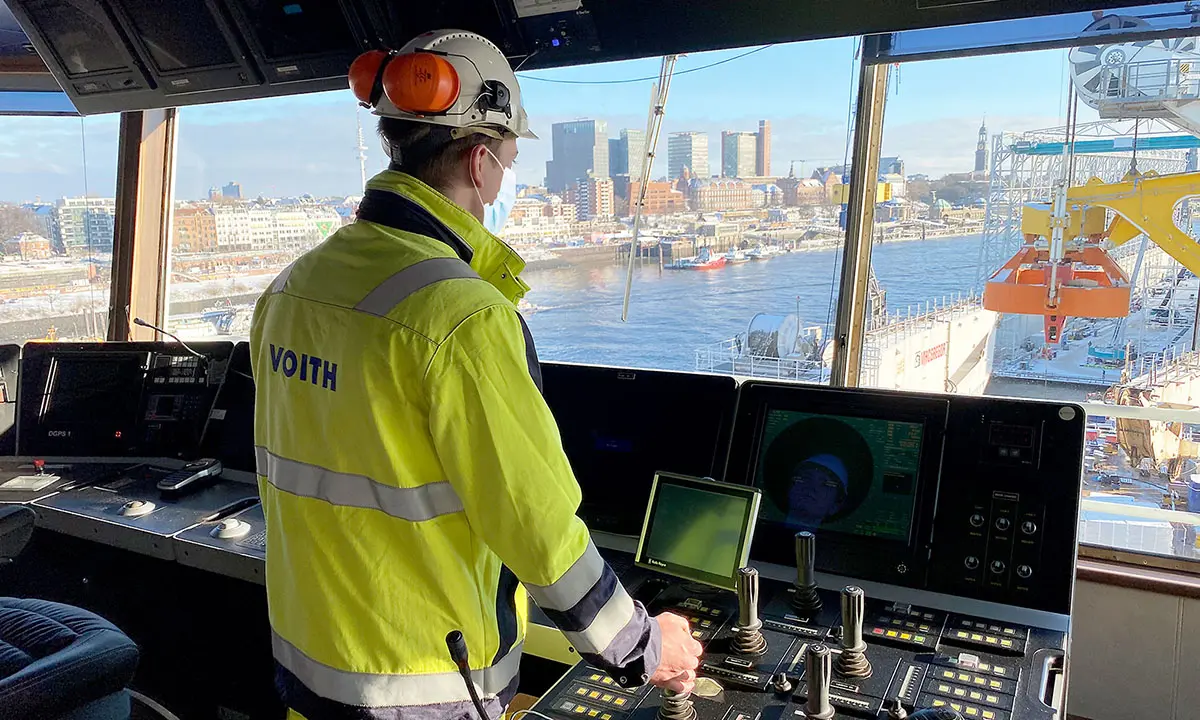
Service performed within and according to schedule
The North Sea Giant now rested calmly in the harbor waters of the Elbe. All VSPs had passed the tightness test. The crew powered up all systems, not least to check among other things that the cooling of the drive units was working properly.
Following this second stage came the crucial stage for Zonneveld and his team, as the propellers started running. He personally watched this start-up phase from the wheelhouse of the North Sea Giant. At this point in time, Zonneveld did not even notice the beautiful view of the Hamburg Port skyline, which was particularly picturesque on this sunny but cold day. He was listening anxiously to the motor and propeller noise. The North Sea Giant moved gradually towards the open sea. The vessel then passed through a short but decisive full-load phase before Zonneveld could relax: “I was so pleased; it was such a weight off my shoulders,” he says. The service contract was now an absolute success for him, too, and had been completed within the schedule.
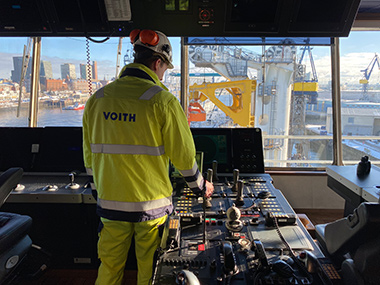
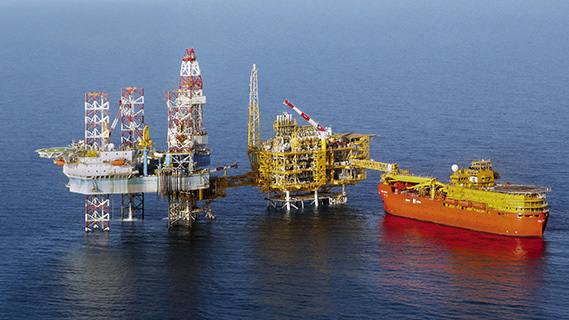