Efficient drive technology for high productivity
DrivAx servo drives are suitable for all linear movements requiring high forces and precision. They consist of a variable speed pump and a servo motor, which simultaneously serves as drive and control for the actuator. DrivAx drives make hydraulics more economical and sustainable. Only the actual amount of power needed for the process is generated from electrical energy. Hence, DrivAx servo drives use up to 80% less energy than conventional hydraulic systems. It’s not just the environment that benefits.
Reduce complexity – increase productivity
DrivAx – compact, powerful,
user-friendly
For more sustainable hydraulics
Saves electricity, oil, and CO2emissions
Hydraulics for today and tomorrow
Welcome to the future – more operating time, less maintenance
Which DrivAx drive is the right one for your requirements?
|
|
Our product video about the hydraulics of tomorrow
Would you like to learn more about our DrivAx product family? In our product video, the Voith experts summarize the most important information for you.
Voith Service – how can we help you?
Every day holds new challenges and we help you master them successfully. Anytime. Anywhere. Please click on the icon to find out more about our hydraulic systems services.
Your service helpline
t +49 7152 992 3
OnCall.Video is Voith’s audiovisual communication system that enables worldwide access to Voith expertise via our web-based video collaboration platform.
Read more
Specially designed for self-contained servo drives, the mobile service and flushing module SFM 20 ensures a high quality and a low error rate of the service work.
More information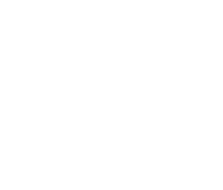