Hydropower will become more important
The “Paris Agreement under the United Nations Framework Convention on Climate Change” clearly stated that global warming must be kept within a maximum of 1.5 °C if one wants to reduce the risk of a global climate collapse. To achieve this goal, steering electricity production toward clean, renewable technologies is necessary.
Hydropower accounts for 14 % of global electricity generation, a greater percentage than all other renewables combined. Of these, it also produces the largest amount of energy, at 64%. Hydropower is a proven, predictable and price-competitive technology that plays an important role in the transition to renewable energy.
The wind and solar industries are also interested in hydropower and pumped storage to firm up their variable generation. With the increasing ability to operate hydropower projects and pumped storage facilities to integrate variable solar and wind, we can move faster and more cheaply to a low-carbon economy. Hydropower is also being given a fresh look in combination with other technologies, such as hydrogen production.
Facts and figures

Learn more about the efficiency and capacities of hydropower plants, the Energy Payback Ratio of hydropower, the power generation capacity from renewable energy sources and how much CO2 could be avoided by using hydropower compared to burning fossil fuels in an animated graphic.
Hydropower is a low-carbon technology

- CO2 and methane are natural GHGs present in the earth atmosphere.
- Each human activity has a GHG footprint – reservoirs and hydropower are no exception.
- Within the global energy mix, hydropower is one of the lowest GHG emitters.
- The huge majority of reservoirs and all with a power density (W/m²) >5 emit less than 100 g CO2eq/kWh.
Hydropower Sustainability Governance Committee (HSGC)
Voith is also represented in the Hydropower Sustainability Governance Committee (HSGC), a multi-stakeholder group that governs the Hydropower Sustainability Tools. With these tools, we can define international good and best practice in sustainable hydropower development and assess project sustainability. Just recently a new certification and labelling scheme for hydropower was launched: the Hydropower Sustainability Standard.
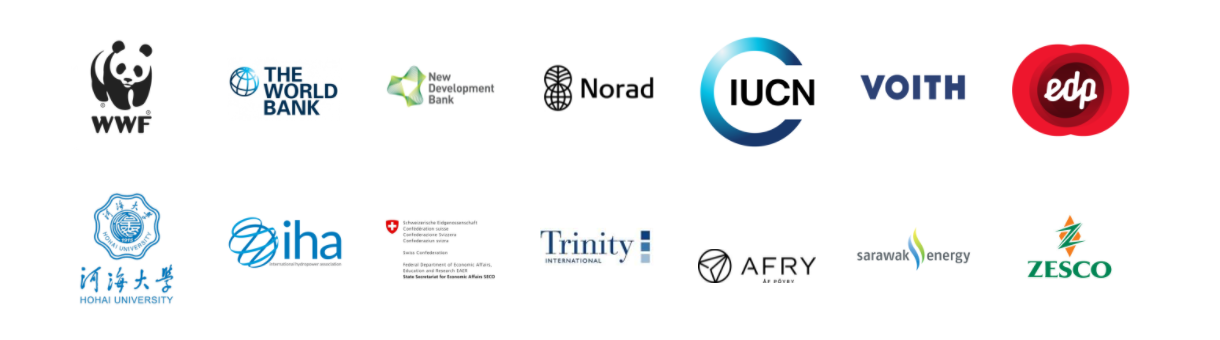
Hybrid and symbiotic concepts offer new opportunities
Hybrid solutions – such as pumped storage power plants combined with wind and/or solar farms – are becoming increasingly important for the generation and storage of clean, renewable energy, as well as in the production of drinking water.
Voith Hydro’s sustainable solutions
Minimizing the impact on the environment
All forms of electricity production require balancing tradeoffs with benefits. Throughout Voith Hydro’s unparalleled industrial experience spanning more than 150 years, the organization has been working to minimize the impact of hydropower on the environment. Specifically, ensuring safe fish passage has been one of Voith’s industry goals since the 1990s, leading the company to conduct analytical and physical modeling in its laboratories. Greaseless technologies have been commonly used to maintain water quality for more than twenty years.
Minimum Gap Runner
Adjustable blade turbines such as Kaplan or Bulb turbines feature blades with varying pitch and are characterized by gaps at the inner and outer blade peripheries. These gaps can give rise to leakage flows, resulting in the formation of vortices. These secondary flows cause elevated water velocity, shear and rapid pressure changes and low absolute pressure levels, all of which are potentially harmful to passing fish.
To minimize the effects of gap flows on fish survival, Voith Hydro developed the Minimum Gap Runner (MGR) technology as part of the Department of Energy’s Advanced Hydropower Turbine System (AHTS) program.
The MGR blades are contoured to a fully spherical hub and periphery so that the design gap remains constant across the pitch range. In addition to the stated goal of improving fish survival, the minimal gap also has positive impacts on turbine efficiencies.
Over the past decade, MGR technology has been implemented at several large axial flow units in the field. Examples are the Grant County (Washington) Public Utility District’s Wanapum Dam, the US Army Corps of Engineers’ Bonneville Dam and American Municipal Power’s Ohio River projects.
Fish survival rates through MGR units have been documented to be in excess of 95%.
Oil-free hubs
Adjustable blade runner hubs are typically filled with pressurized oil. This oil lubricates runner blade trunnion bearings and sliding parts of the operating mechanism in the hub. However, using hub oil endangers water pollution by oil spill from the hydroelectric facility. In order to eliminate this risk, Voith Hydro has been developing and installing oil-free solutions since 1985.
Pressurized oil has been replaced by self-lubricating materials and assures not only the prevention of accidental releases of grease substances into the environment but also allows for easy maintenance, lower friction and good bearing performance without the necessity of increasing servo size.
Aerating turbine technology
Over the years, Voith Hydro has become a leader in providing aeration solutions that improve environmental compatibility through the increase of dissolved oxygen uptake downstream of hydropower facilities. These advancements address a common issue faced by hydropower producers: the need to improve water quality, specifically dissolved oxygen content, as water is discharged from existing and new hydroelectric equipment. The water in the lower reaches of many reservoirs is oxygen deficient.
Often, low pressure regions below the runner can be utilized to draw atmospheric air into the turbine during operation. These machines are referred to as auto-venting turbines (AVT) and are particularly cost-effective for injecting large quantities of air into the discharge.
Auto-venting turbine aeration generally consists of three different aeration options, including distributed, central and peripheral aeration.
The interaction between the incoming bubbles and the surrounding water drives the aeration performance by influencing the pressures at the air injection location, the resulting air flows, the dissolved oxygen uptake efficiency, and the turbine performance.
For each project, individual site characteristics, plant design, and desired operation are incorporated into in-house calculation methodologies which account for the necessary bubble modeling to optimize aeration behavior. Based on the predictions, Voith Hydro selects aeration solutions which provide the best value for the customer by maximizing uptake while minimizing the impact on turbine performance and aeration costs.
Alden turbines
One of the newest improvements to fish passage technology comes through development of an innovative runner concept by Alden Research Laboratory. The Alden Turbine features a slower rotational speed and only three blades to reduce fish mortality due to blade strike. Voith Hydro has optimized the final design and tested it at their hydraulic laboratory in York, Pennsylvania (USA).
The blade shapes are specifically designed to improve the fish passage environment through the turbines by minimizing shear, pressure change rates and minimum pressures within the water passage. Depending on the species, full-scale fish survival rates are expected to range from 98% to 100%.
Through funding made available by the DOE, EPRI and industry partners, Alden Research Laboratory collaborated with Voith Hydro to improve the performance characteristics of the conceptual turbine while maintaining or improving the fish-friendly characteristics. The partnership also focused on ensuring the turbine’s cost-effectiveness while maintaining improvements in fish survival rates.
Key benefits:
- Reduced strike probability by optimizing the number of turbine blades, wicket gates and stay vanes as well as improving the hydraulic profile of the turbine components and the rotational speed
- Optimized water passage geometries to meet specified fish passage criteria
HyCon GoHybrid
The HyCon GoHybrid is a highly innovative and efficient, hydraulic power unit with a particularly compact design to enter the next-generation of governor systems. Standardized components reduce maintenance costs for operators.
The oil system’s reduced complexity lowers the required oil volume by up to 60 percent compared to conventional high-pressure units and by up to more than 90 percent when measured against low-pressure units, thus providing a more environmentally friendly solution. The HyCon GoHybrid is a state-of-the-art concept that goes beyond the common technical specifications and conventional rules.