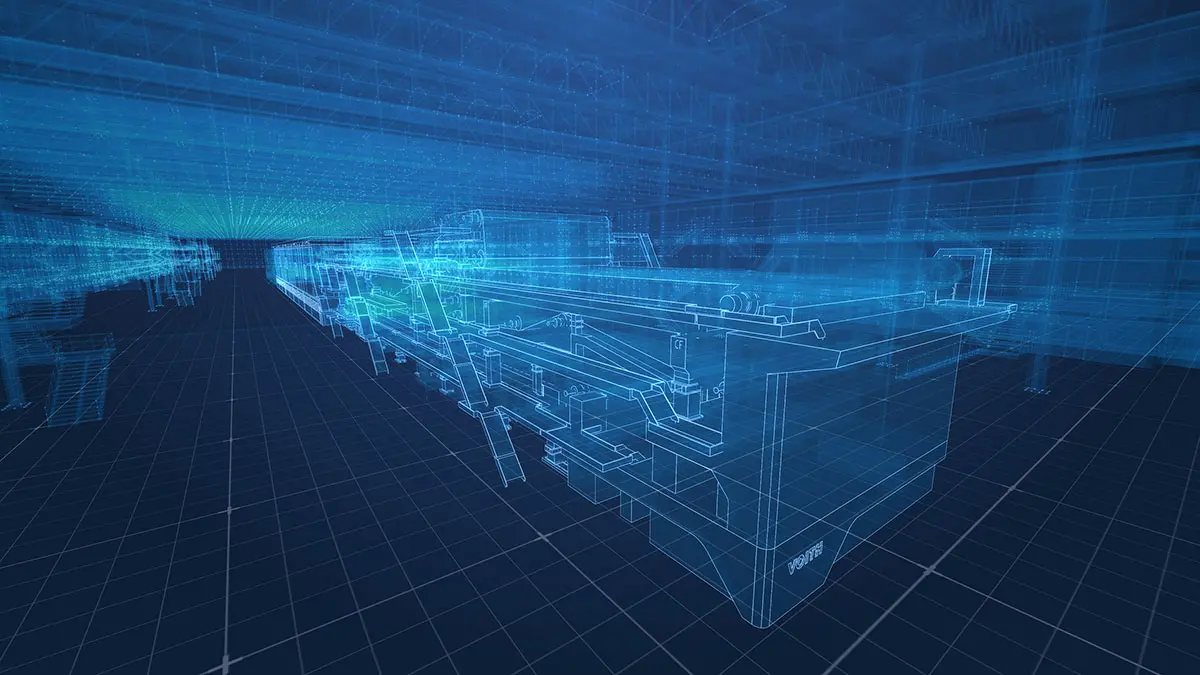
Digitalization
The digital paper mill
12th November, 2020
After successfully digitizing its paper mill in Venizel, France, Saica Paper now also wants its mill in El Burgo, Spain, to become more digital. We spoke to Fernando Carroquino, Industrial Director at Saica Paper, about the experiences he has made since our last interview in 2017 and how the coronavirus pandemic has changed the way the paper industry perceives digitalization. Due to the corona pandemic and in line with the topic, we conducted the interview virtually.
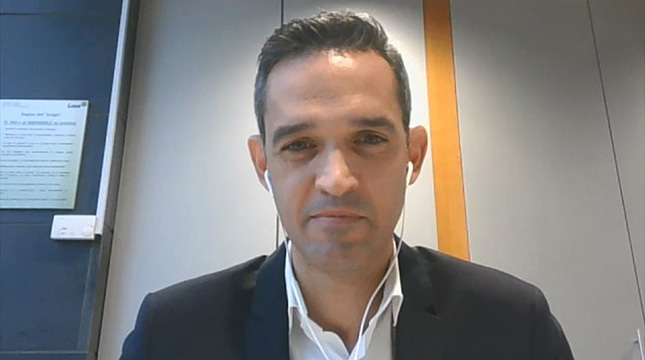
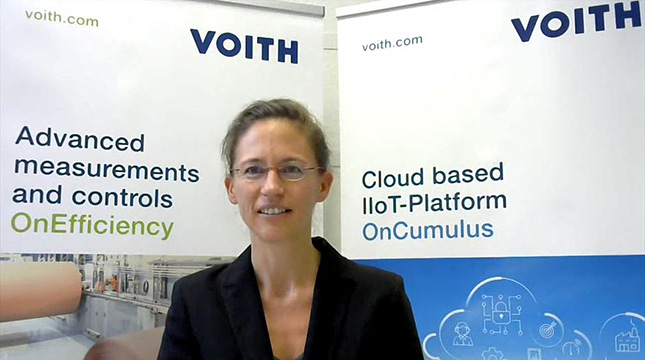
Three years ago, we spoke about opportunities arising from digitalization. How do you assess the situation in the paper producing industry today?
There are exceptions, but generally speaking, the paper industry is very traditional and often skeptical about new things. We'd rather invest in steel and big machines than in computers and algorithms. It is therefore very difficult to present new ideas within this community. My feeling is that it will take time to make a global transition to a more digital paper production. There are some developments and investments in digitalization, but only to a limited extend. So, the digitalization of the paper industry is progressing very slowly, step by step.
How has the corona pandemic changed the way the paper industry perceives digitalization?
This pandemic has not been a conventional crisis as the one in 2009. From an economical point of view, crises usually spread rather slowly and predictably. In this case, however, each month and week is completely different. Digitalization can help us to adapt our raw material stocks to the constantly changing market requirements and to use the available materials as efficiently as possible while meeting the same paper quality.
I am sure that there has been a change in mindset in different cases. Due to the current situation, we had to carry out some minor commissioning remotely without having a responsible technician on site. In the past, I would have said this was impossible, and I would have preferred to have someone on site. However, as the current circumstances do not allow this, the digital tools have become absolutely necessary.
Of course, the personal contact is important for professional relations, but we have changed completely. We even schedule internal online meetings between our paper mills that are not far from each other. So I do not think that we will go back to the same point we were in the past. We are even more connected than before and that also carries some risks. Cyberattacks will become one of the big issues in the future. In the past, we could have just cut the connection. But today, we depend on the Internet. Cybersecurity should therefore have top priority in digitalization.
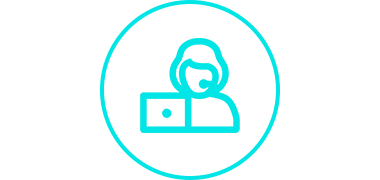
With the audiovisual communication system OnCall.Video, customers can access Voith's expert knowledge worldwide, regardless of time or location.
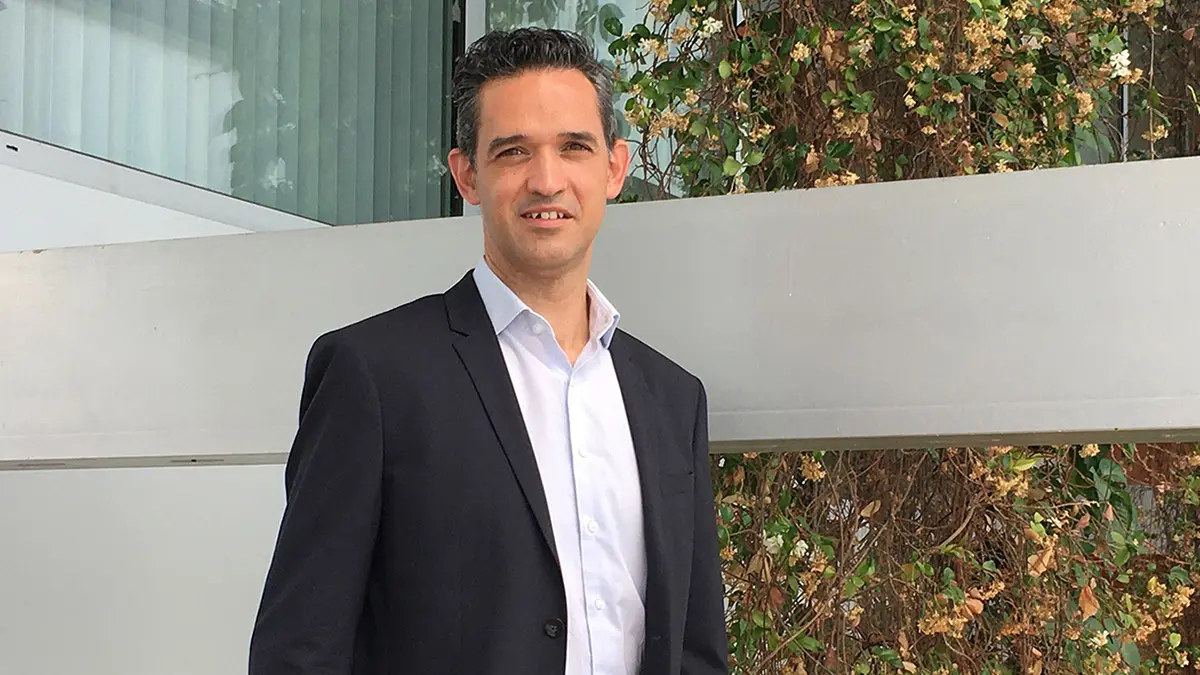
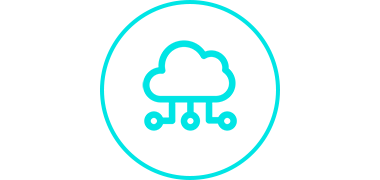
Voith’s IIoT platform OnCumulus serves as a hub for data from multiple sources – and with help of several apps, this data is turned into actionable information.
Which topics should the paper industry deal with first when talking about digitalization?
In the past, we have tried to perfectly adjust a paper machine to produce certain types of paper grades. This paper machine was in a comfort zone when producing what it was prepared for. But now the market is changing very fast and we should be able to flexibly adapt our production to the current demand. Digital tools could be a great help here. They will not transform a slow paper machine into a faster one, but they can provide the most efficient way to produce a specific paper grade based on real-time data. To make this possible, paper manufacturers should start by equipping their machines with sensors and collecting data.
Do you think a stronger value chain integration with individual information about the customers and suppliers would be helpful?
To be honest, that sounds too big for me. It would certainly add value to the entire supply chain. If we knew, for example, that there was an increasing demand for a certain type of packaging paper, we could probably react earlier and also go back in the value chain and already place an order for a certain type of waste paper. In reality, however, we are divided into different departments. On the one hand we have the customers and on the other the suppliers. So it would be very difficult to integrate and manage this internally. I think we should try to produce the best possible paper with the resources that are available to us. That's why we need to make faster progress with the digitalization of our production lines.
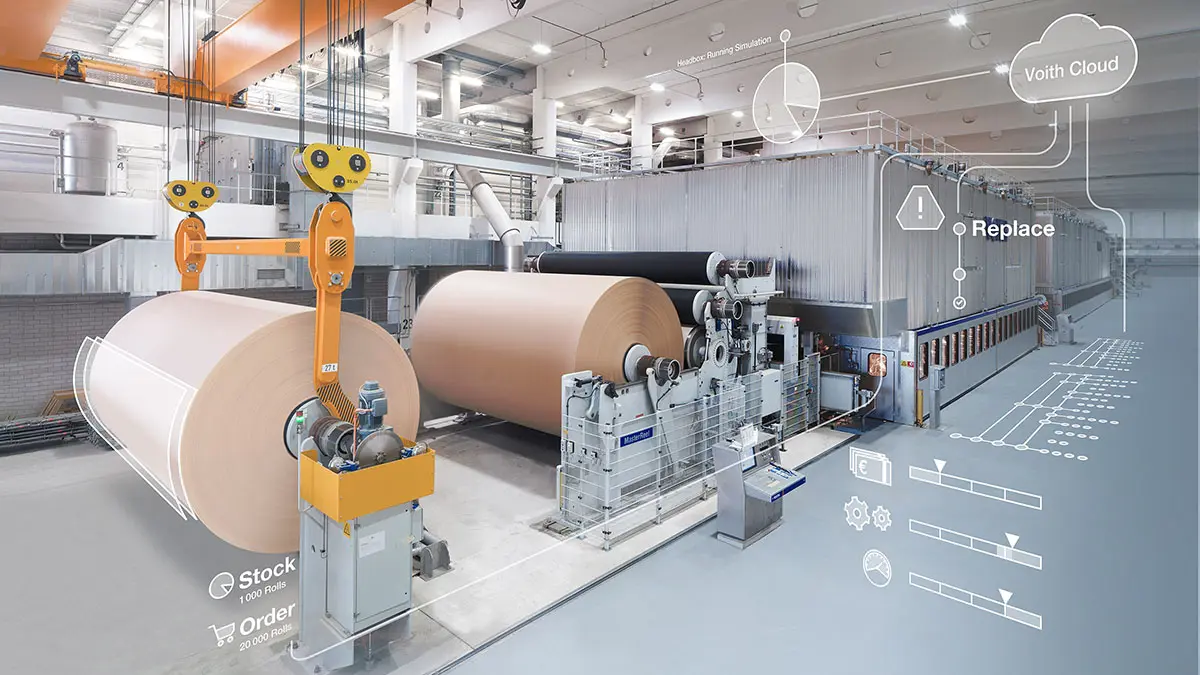
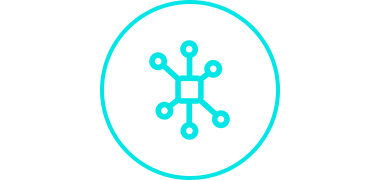
OnEfficiency.BreakProtect uses a unique AI algorithm to detect critical process situations and display specific countermeasures how to prevent a break.
What are the major challenges in implementing new digital tools?
From my point of view, one of the biggest challenges is to convince your employees of the new tools. A good example is break prediction. When the system predicts a break in 10 minutes, without saying which parameters would need to change to prevent the break, the only thing the operator can do is to be prepared for the break. There is not much he could do, so this could cause more frustration than being helpful. If the system defines countermeasures, and the operator follows them, how does he know whether there really would have been a paper break? In the end, it is impossible to say whether the improvements are due to the operator or the system. That could generate an inner rejection against such a break protector. The applications should therefore offer the operator specific instructions and give him the feeling that he successfully prevented the paper break with these measures.
This persuasion takes some time. You need someone who is absolutely convinced and who pulls the others along. However, this will only work if the tools are completely developed and easy to use. Digital paper machine applications should be as simple as an application on your mobile phone. If the people find it difficult to use, they will not end up using it. The new visualization of OnView.MassBalance fulfills exactly this requirement, and I really like it.
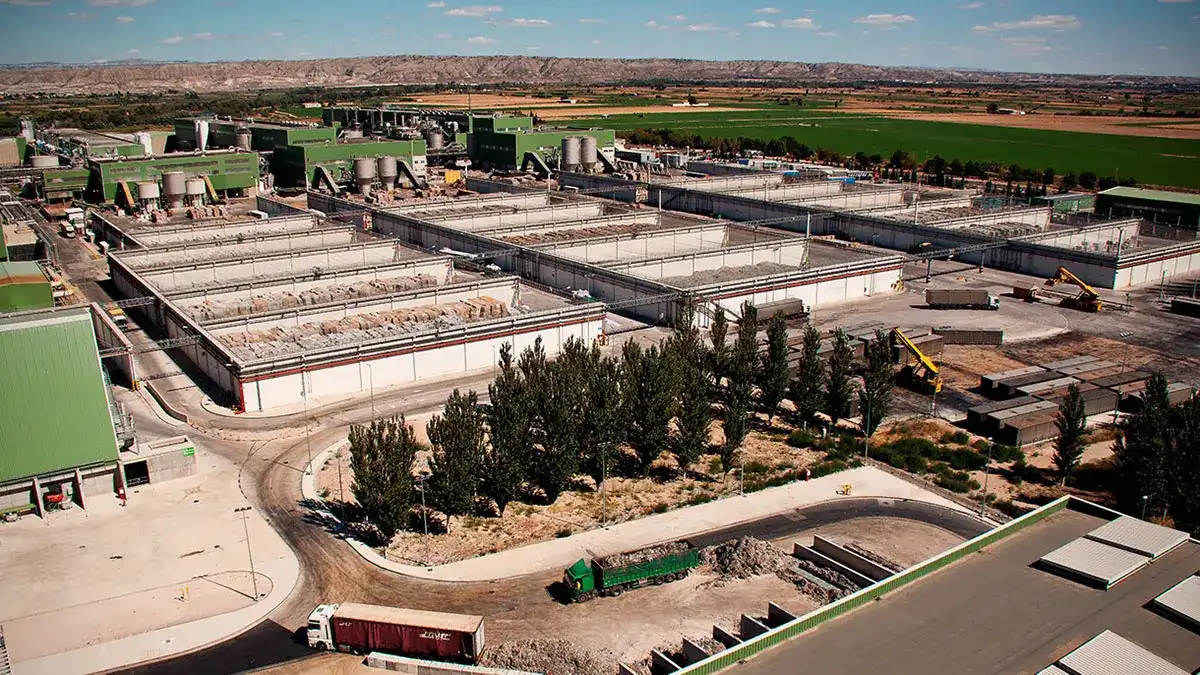
You have already successfully implemented some digital tools at the paper mill in Venizel. What challenges did you face and how did you tackle them?
Our major challenge is that the customers always expect the same paper quality. The problem is that the quality of our raw materials varies a lot. We should always be able to produce the same product, no matter what material we use. So the most important area to deal with was therefore the stock preparation. If we are able to stabilize the quality of the pulp we put into our machines, we will have less variation in the end.
At the moment, the system is giving information and we use it for improving, but the idea is that little by little we should start to close some loops in the stock preparation plant, and at this moment we should see a bigger improvement in efficiency of this area.
What has changed so far?
I think we are more open minded to digital solutions. Before we introduced the new tools in Venizel, we were highly sceptical. We thought we would have to feed the key parameters into the system, but now the system is starting to tell us which parameters need to be adjusted. We are all very good papermakers, but we are not able to analyze thousands of parameters at the same time and come up with the most efficient solution. The people start to see the advantages of digitalization. I wouldn’t say this process is finished, but it is a good development.
Imagine a paper mill in 10 years from now. How will it look like?
When I imagine a paper machine in 10 years, it will offer more support; we should have a more friendly paper machine for our people. Algorithms will help operators by telling them what to do in case of a problem, such as too many paper breaks. These tools will be standard, because even good papermakers need good tools for increasing efficiency over 92%. People are very important, but it is impossible to have an absolute expert in every area on every shift. The digital tools will help to solve all the small daily problems. One day our papermakers might say: “Well done, Algoritmo!”
Thank you for the interview!
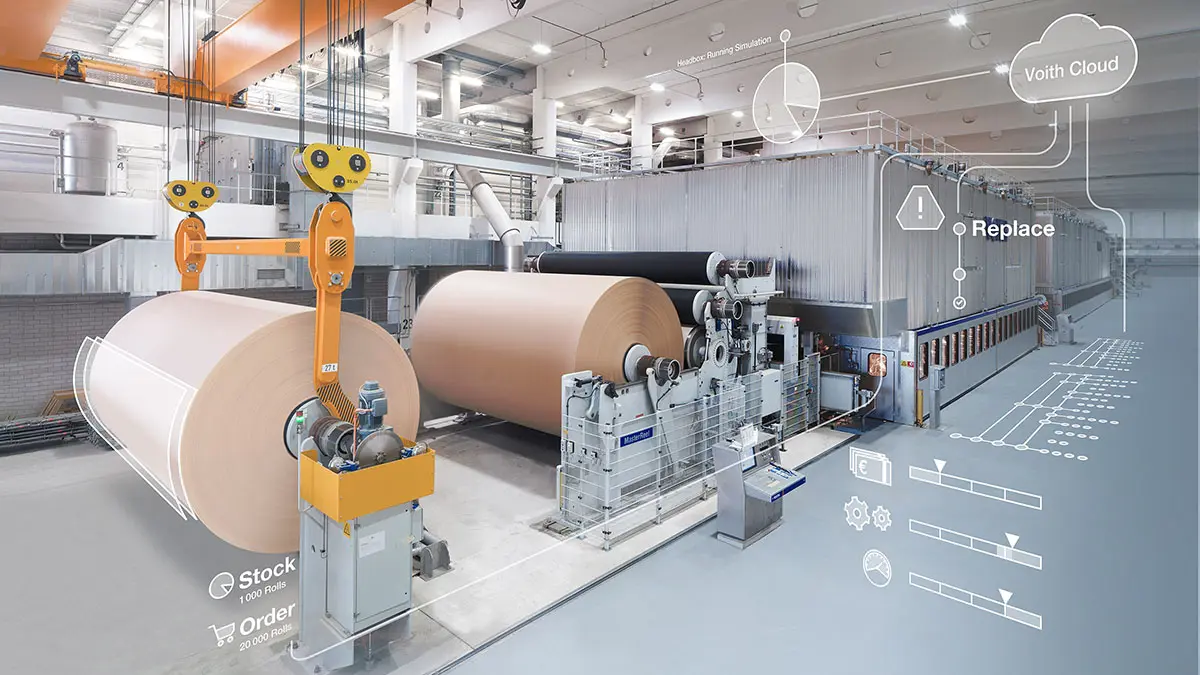