Got a strange problem? Voith Turbo offers straight service.
The best service is the one that has seen it all before. We can live up to this statement: Our experts are knowledgeable in many industries and applications. With our long-standing experience, nothing surprises us anymore. And if there is a problem we haven’t encountered before, we will be the ones that find a solution! Find the contact who can best support you with your problem.
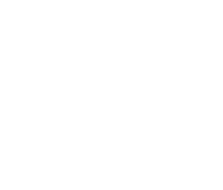
Find your contact
Our service offerings
To solve even the most unusual problems and challenges, you will need a very special portfolio.
Our services will prepare you for anything! You will be able to focus completely on your core business, while Voith supports you with comprehensive services as a full-service provider. Whether for a Voith or third-party brand, our service experts visit you worldwide onsite and always keep the availability of your fleet front of mind.
Special knowledge from unique people
Read here how our service teams can help you in your industry.
Show all publications
-
-
High performance synthetic lubricant for final drive units | V Gear Synth Plus SAE 75W-90
PDFEnglish
Software solutions
Cloud solution Aladin
Aladin Beyond
The future of maintenance is data
Benefit from our decades of experience with a groundbreaking tool for all Voith products. Experience our intuitive, data-driven maintenance and get your Aladin Beyond report now!
Get your Aladin report
Detailed analysis:
DIWA diagnostic software Aladin download
To download our proven Aladin software diagnostic tool, please fill in the form.
We have send you an email with the download link.
Something went wrong. Please try again later.
OnCare.Asset Rail
Efficient management and information are the key roles for successful implementation and optimization of costs and service
The OnCare.Asset Rail Life-Cycle-Management System continuously accompanies the life cycle of vehicles, fleets and their components. The retrieval of economic and technical data via the OnCare.Asset Rail Internet portal shows trends at a glance and ensures the transparency that is required for ongoing optimization.
- Supervision and tracking of vehicle fleets
- Implementation of maintenance
- Condition Monitoring
- Vehicle and process optimization
OnCare.Asset Rail allows to identify weaknesses and introduce targeted measures, so that technical failures are reduced while the availability, reliability and safety of your vehicles and/or fleets are increased while taking into account documentation responsibilities.
Logistics and communications become more efficient, as all relevant information including current operating, diagnosis and position data is at your disposal. You are directly integrated into the planning and maintenance process.
Key benefits:
- Reduction of maintenance costs
- Minimization of downtimes and failures
- Optimization of maintenance concepts